» Sponsors |
Support Our Sponsors |
|
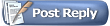 |
03-30-2007, 01:14 PM
|
#1
|
Registered User
Member
Join Date: Mar 2007
Posts: 30
|
modern traction bars part 1
How to build modern Traction Bars
For leaf spring cars and trucks
Traction devices have been around for years. Perhaps the best known are the classic "traction bars" that bolt to the bottom of the springs and / or axle. As the axle tries to rotate under acceleration, these bars contact the underside of the spring and help stop the pinion gear from trying to climb the ring gear and in the process provide a modest increase in traction. See figure 1. Although these devices aren't 100% effective they do work pretty well.
Figure 1
On a street rod or vehicle that may have less ground clearance than your ordinary muscle car this type of traction bar may present a serious problem. Not only in ground clearance but these bars can stiffen the suspension considerably and provide less comfort for the passengers.
Theory
When it comes to a streetable traction device what is needed is something that limits wheel hop, prevents spring and axle wrap, and increases traction. But that's not enough, it still has to allow the suspension to move and work as designed so comfort and derivability aren't adversely effected.
Perhaps the best idea so far is what has commonly become known as "Caltrac Traction Bars". Caltracs are made by Calvert Racing a company in Lancaster, California and represent probably the most cost effective way to transfer the rotational energy created by the axle to down force on the suspension which definitely improves traction. This design transfers this rotational energy through a bellcrank system and actually pushes down on the spring instead of up as on the classic traction bars of the past.
Since they are generally designed for high horsepower applications, Caltracs are very heavy-duty devices and can in this writer's opinion be rather expensive. Since most of us aren't driving a 600 + hp Sportsman Class race car on the street, at least not for everyday driving, we don't need the "heavy duty" aspects of Caltracs but we still want all the benefits they provide. The solution is simple.
Building your own version of the classic Caltrac design isn't as hard as you may think and it only requires the basic tools any "gearhead" will have around the garage and chances are if you don't have what you need, you have a friend who does. Now I'll be the first to admit that I'm no engineer but I do know what works. This system has been proven by some pretty big names in pro-stock drag racing and that's more than enough proof that this concept works very well.
How they work
Before we get started let's look at what these bars are designed to do. (See figure 2)
Figure 2
Under acceleration the axle naturally tries to rotate. This "climbing of the pinion gear on the ring gear changes the pinion angle and general geometry of the suspension. In many cases it causes the spring to deflect or "wrap up" (see figure 3) which increases the change in pinion angle (among other things) and complicates matters even more.
Figure 3
To effectively eliminate these problems the rotational force of the axle must be redirected or transformed to a force that helps weight transfer and traction. This bellcrank and rod traction system directs the rotational energy created by the axle through a rod to a bellcrank located on the front spring eye. There the energy is converted to down force on the front of the spring where it is weakest. This eliminates spring wrap and at the same time helps to force the suspension to the ground providing an increase in available traction. Simple but extremely effective.
Tools and Materials
You'll need a grinder, saws-all or similar device for cutting 3/16" steel plate, a welder, and a good drill or small drill press. Materials are easy. Just run down to your local scrap metal yard and pick up a piece of 3/16" steel plate about a 1'x 2' and 8 feet of ¾" ID (1"OD) steel pipe. You will also need about one foot of 5/16" ID steel pipe. To connect the brackets and bellcrank you'll need (4) ¾" rod ends and 8 matching nuts along with a total of at least (4) ¾" bolts and nuts, (8) ¾" washers along with (2) 5/16" bolts, nuts and 4 washers. The length of these bolts will be determined by your specific application so it's best to make the brackets first and then measure for bolt length once you test fit them on the car. The big advantage of building your own traction bars is obvious. It can easily be done in a weekend and the cost will be well under a hundred bucks. Not bad when you consider the price of the real thing.
Construction
The first brackets you need to make are for mounting the force transfer rods to the bottom of the spring retaining plates. (See figure 4) On most applications mounting the rod at a point 2" below the plate should allow enough clearance for the rod to connect to the front bellcrank without interfering with the spring. Be sure to check this before spending the time to make brackets that might be too short. Start by measuring the distance from the front spring eye to the first spring. Take half of that measurement and it will tell you how far below the spring eye bolt the rod will attach to the bellcrank. On average this measurement will be in the neighborhood of 6". The rod should be able to miss the springs by at least 1". If it doesn't, these lower brackets will need to be a little longer.
<H3>Figure 4
You will need to make four of these brackets and drill a ¾" hole in each. They will be welded to the bottom of the spring mounting plate with the attachment hole directly centered under the axle.
Now we need to turn our attention to the bellcrank. You'll need four identical pieces here too. The first thing you need to do for the bellcrank is to determine where the spring is going to deflect or wrap up the most. In this case use the same measurement you used previously. Half of the distance from the front spring eye to the first spring. This is the spot where the spring is a single leaf and is weakest and this is where you want to put down force on the spring to keep it from wrapping up under acceleration. See figure 5.
Figure 5
To keep the forces equal the bottom hole of the bellcrank should be the same distance from the pivot point as the pressure point. In this example the measurement from the spring eye to the second spring was 12". We use half that measurement (6") to determine the length of our bellcrank. (See figure 6) Don't forget that you need 4 identical brackets.
Figure 6
The transfer point hole needs to be ¾" to accept the rod end and the pressure point hole should be a minimum of 5/8". In our example the pivot hole diameter should be 1" because the current bolt size is 3/4" and we'll be using a piece of scrap 3/4" ID (1" OD) tubing left over from cutting the transfer rods to length as bearings for the bellcrank. Your application might be slightly different so the hole size you drill in the bellcrank might be smaller. What you are shooting for is to use a small piece of tubing with the same ID as your bolt to act as a bearing for the bellcrank. If your bolt is 9/16" then use that size ID tubing for the bearing and drill the hole in the bellcrank the same diameter as the outside diameter of the tubing you're using. The fit doesn't have to be exact but you don't want very much slop either. See figure 7.
Figure 7
Once all the brackets are completed, weld the small brackets to the lower spring mounting plates with the ¾" hole centered under the axle and from side to side. Remember to leave enough space between each bracket to mount the ¾" rod end and a washer on each side. Don't forget these washers, they're important. The best method I've found is to temporarily mount a rod end with its two washers and tack weld the brackets in place. Then remove the rod end and finish welding the brackets. It is easier to remove the mounting plates for this job but it can be done on the car if you don't mind welding in that position. When you're done the lower spring mounting plate should look something like this. (See figure 8)
|
|
|
03-30-2007, 01:15 PM
|
#2
|
Registered User
Member
Join Date: Mar 2007
Posts: 30
|
part 2
|
|
|
03-30-2007, 05:00 PM
|
#3
|
Registered User
Moderator
Join Date: Jan 2005
Location: East side!!!!!
Posts: 6,430
|
Nice write up!
Good job
__________________
I have no car-
|
|
|
03-31-2007, 06:40 AM
|
#4
|
Registered User
Member
Join Date: Jun 2006
Location: Waterford
Posts: 185
|
kind of like make your own slide a links or caltracs....
I use the slide a links and they work really well. If I saw this post prior to buying them I would have tried to make them myself...oh well.
__________________
Rob Dunn
2000 Dakota RT
12.2 @ 105 mph
|
|
|
12-10-2008, 08:56 PM
|
#5
|
Registered User
Member
Join Date: Nov 2008
Posts: 1
|
Don't quit your day job!
|
|
|
12-20-2008, 07:29 AM
|
#6
|
Registered User
Moderator
Join Date: Jun 2006
Location: Highland, Mi.
Posts: 581
|
Not sure if you did it yourself, but cool write up.
Don't pay attention to this BoostCreep guy. He's just a player hater.
__________________
1984 Capri. Finally at home, slowly coming together??
|
|
|
07-21-2011, 09:35 AM
|
#7
|
Registered User
Moderator
Join Date: Apr 2007
Posts: 37
|
Way to STEAL the credit for these LUNGER.....
|
|
|
07-21-2011, 11:07 AM
|
#8
|
Registered User
Member
Join Date: Mar 2007
Posts: 30
|
HMMMMM don't see anyplace where i took credit. I wanted to be like you rickety, since every thing you have done to your cars over the years is just a copy of what Boostcreep did first.
Last edited by Rickety; 07-21-2011 at 12:11 PM.
|
|
|
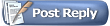 |
Posting Rules
|
You may not post new threads
You may not post replies
You may not post attachments
You may not edit your posts
HTML code is Off
|
|
|
|
» Links |
DR Links |
|
|
All times are GMT -5. The time now is 04:49 PM.